Application areas
Our machines are successfully used at ship-repair, ship-building, oil and gas enterprises and by other companies specializing in anticorrosive treatment.

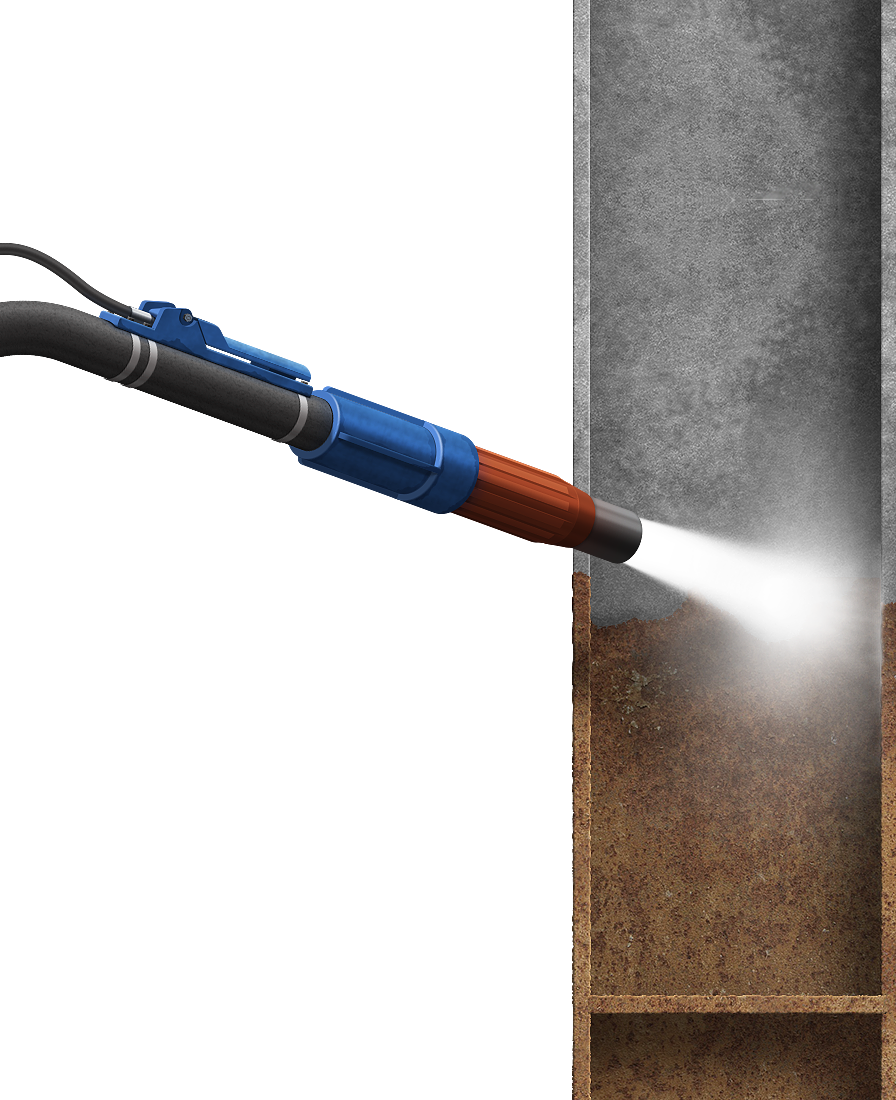
Operating principle
The flask is filled in with the abrasive material, the water is automatically pumped in proportion of 3 parts of abrasive and 1 part of water. The wet abrasive material with performance of 20-35 m²/h rubs off the rust, old paint and other contaminations. Preparation grade Sa3, Ry=40-80 µm (up to 270 µm depending on abrasive sizing), dust content 0 point, salts less then 100 mg/sq.m or less than 50 mg/sq.m
Flask
- Hydro tests have been completed, ultrasonic testing of welded butt joints has been carried out according to STO 00220256-005-2005.
- Each flask has a passport.
- The flask is equipped with wheels and handles that facilitate movement of the apparatus at the work site.
- For loading and unloading, use the mount at the top of the flask.
Characteristics
- Flask walls thickness
- 6 mm steel
- Operating pressure
- 1,2 (12) MPa (kg/sm²)
- Calculated pressure
- 1,2 (12) MPa (kg/sm²)
- Test pressure
- 1,5 (15) MPa (kg/sm²)
- Working temperature
- +5…+35°C
- Minimal flask surface temperature
- -20°C
- Name of the working environment
- pulp abrasive material
- Corrosion compensation supplement
- 2 mm
- Volume
- 0,3 and 0,08 m³
- Estimated lifetime
- 20 years
Main regulatory documents
Control cabinet
It includes a system of pneumatic electric control and air distribution, switching sockets of the operational control path, a manometer measuring the air pressure in the system, a pneumatic diaphragm water pump, and an air filtration unit.
Control key
Electric Control Key — control system element, which allows you to quickly disable the abrasive in the tract. Cable length in the package 10 m. Can be equipped with an additional 20 m cable.
PT abrasive valve
Designed to feed abrasive into the abrasive path, quickly shut off the abrasive feed and adjust the amount of abrasive feed into the path.
It differs from the traditional sliding gate by speed of response to the control action "On / Off", determined by the speed of operation of the electric line. This method of controlling the flow of abrasive is considered the safest.
The working element used to shut off the abrasive feed is a boron carbide plunger pair - a bushing and a finger.
Drainage (air path)
Designed to control the flow of air into the apparatus and is equipped with emergency valves that allow you to quickly open and close the air supply. The presence of valves increases the safety of operation and eliminates the insurer. Additionally, it can be equipped with an input gearbox.
Water path pipeline
Designed to supply water (inhibitor solution) to the flask and (or) the air path. Provides control of the amount of the supplied solution and the amount of memory.
Volume
Changeover time
Production
cycle
Working pressure
Cleaning speed
Abrasive consumption
Process performance comparison
Surface corrosion damageВ, С (ISO 8501-1)
Roughness of the cleaned
surfaceSa = 2,5 (ISO 8503-2)
Abrasive path length20 м
Due to the increased load volume, an increase in the Energy Blast-300 performance occurs, which prolongs the service life of the components. And the increase in working pressure of the device reduces the consumption of abrasive material.